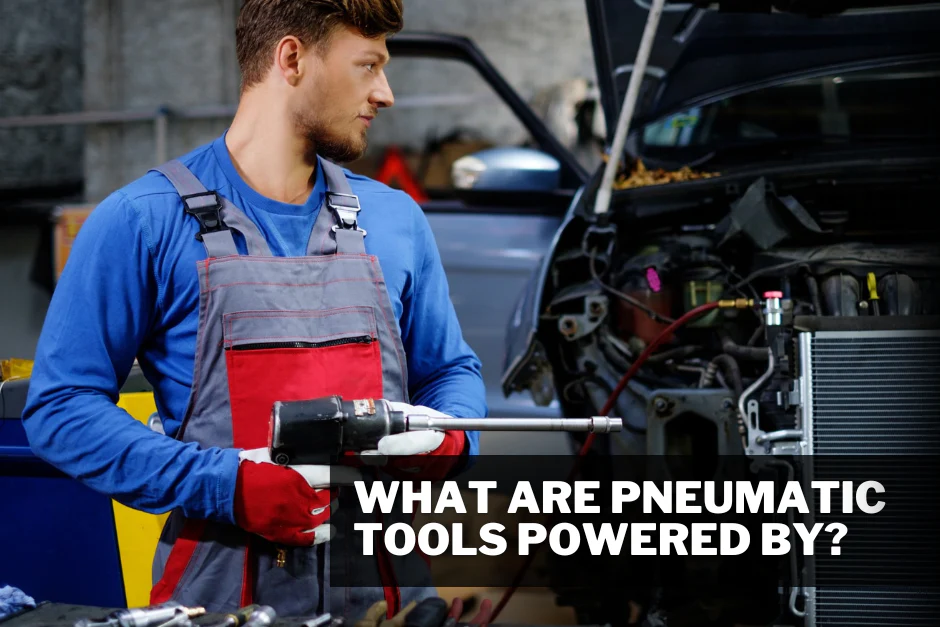
What Are Pneumatic Tools Powered By?
Have you ever wondered what your most handy construction tools are powered by? Click here to learn about what powers pneumatic tools.
Keyword(s): Pneumatic Tools
Studies show that musculoskeletal disorders for most newly reported work injuries account for 33% of on-the-job illnesses. Companies and professionals in labor-intensive industries use pneumatic tools to reduce the occurrence of these kinds of injuries over time.
If you’ve been considering pneumatic tools for your company or trade, you may wonder how they’re powered. Today, we’ll look at the basics of air tools. We’ll also examine what air tools are available. What’s more, we’ll go over how to use them with an air compressor.
Keep reading to learn more about what powers pneumatic tools.
How Pneumatic Tools Work
Pneumatic tools and air tools are one and the same. They’re powered by compressed air.
Air tools aren’t like conventional tools. Conventional tools receive power from electricity.
Air Tool Terms
First, you’ll need to understand some basic terms related to air tools. For instance, if you’re curious about the word pneumatic, it simply refers to compressed or pressurized air.
You should also familiarize yourself with the term CFM. CFM is cubic feet per minute. It’s the amount of compressed air an air compressor can supply or that a tool needs.
You should also understand pressure as it applies to air tools. An air compressor squishes air to a fraction of its value and stores it in a tank.
You’d measure this pressure in bars, pounds per square inch (PSI), or kilopascals. These measurements correlate as follows:
1 bar = 14.5 PSI = 100,000 Pascals (100 kPa)
More Air Tool Terms You Should Know
BSPT, or BSP, means British Standard Pipe Thread. Even countries that use the metric system use the Imperial BSPT standard for air tools, except for the US.
US manufacturers use the NPT standard, which stands for National Pipe Thread. The NPT standard is an inch-based thread.
You should also understand the term gauge as it applies to air tools. The gauge is the size of a fitting or the internal diameter of a hose used for air tools.
Powering Your Air Tools
The air compressor is what squeezes air into a fraction of its normal volume. Once the air compressor does its job, the air takes up eight to ten times less space.
When the compressor squeezes the air, it increases its volume and pressure proportionately. In other words, if the compressor squeezes air into a space that’s eight times smaller, the pressure will increase eight times higher.
Boyle’s Law describes this phenomenon. It states that with constant temperature, the pressure of a gas is inversely proportional to value. The formula for this law is:
PV = constant
When air remains the same temperature, pressure increases as volume decreases. Conversely, when pressure decreases, volume increases.
Compressed Air in Action
Most often, you’ll see reciprocating compressors in workshops. They use a cylinder and piston.
An electric motor or gas engine drives the cylinder and piston. These components work together to compress air.
Once the compressor does its job, it feeds the compressed air into a storage tank. The tank serves as a reservoir.
Now, the storage tank can serve large pulses of compressed air when needed. In this way, a compressor system can serve more compressed air as opposed to if there were no storage tank.
Benefits of Pneumatic Tools
The top advantage of air tools is that they have a high power-to-weight ratio. Air tools are lighter than professional cordless and corded hand tools of the same rating.
An air tool has a simple air motor or piston. These components are lighter than the components in professional electric power tools.
This kind of benefit is vital for assembly-line workers, for instance, which use a power tool all day. A lighter power tool offers the advantage of creating less fatigue.
Also, air tools have a simple construction compared to electric tools. There’s less that can go wrong with air tools for this reason.
Precision Control and Safety
You can stall an air tool indefinitely. Alternatively, the electromotive force of an electric-power tool drops to zero when you stall it.
Also, the current that flows through the motor gets very large. If you don’t release the trigger right away, the motor can burn out quickly.
In addition, professional electric power tools have a universal motor that can run on AC or DC power. The motor produces sparks at the brushes of the commutator.
Alternatively, air tools don’t produce sparks. They provide an advantage in hazardous environments. For example, they’re safer to use around gas and flammable liquids.
Examples of Air Tools
There are many kinds of tools you can pair with an air compressor. In fact, just about any tool you use most likely has an air-powered equivalent. Let’s look at a few tools you may find in a garage, for instance.
Impact Drill and Driver
Just as with standard power tools, you’d use an impact drill and driver with driver bits. This combo makes it easier for you to do dozens of routine jobs.
Air Hammer
If you work in a trade, you’re probably in pretty good shape. Still, an air hammer allows you to do the same amount of work without using up your energy.
Air Die Grinder
You can use a variety of small rotating tips with an air die grinder. This equipment lets you grind, sand, machine, and polish surfaces.
Angle Grinder
You can use an angle grinder to cut, sand, and machine surfaces. Most often, tradespersons use an angle grinder to cut metal.
Air Blow Gun
You can use an air blow gun to remove dust, dirt, leaves, and sawdust. This air tool is ideal for removing debris from large areas, like service bays.
Sanders
Sanding is one of the most tedious jobs in a shop. A single sanding job can take hours.You can get the job done much faster with an air sander. There are different kinds of air sanders, including:
- Belt
- Dual-action
- Random orbit
These sanders are among the most popular air-powered tools in garages.
Pneumatic Paint Sprayer
A pneumatic paint sprayer works with a paint vessel. Before you can use one, you must prepare the surface. However, an air-powered paint sprayer makes painting much simpler than doing so by hand.
Air Polisher
Painting surfaces requires many rounds of sanding and painting. When you’re done with these steps, however, you’ll need to polish the surface to finish the job.
An air polisher saves you a ton of elbow grease. It’s a rotating polisher that takes the hard work out of getting the job done.
Air Nibbler
An air nibbler is two tools in one—a saw and a punch. Instead of cutting metal, you’d use an air nibbler to slowly eat away at metal by biting away at it in pieces.
Air Needle Scaler
An air needle scaler is an excellent tool for agitating and breaking away rust. For instance, a mechanic may use an air needle scaler to remove rust from a car frame.
Air Cutting Tools
Air cutting tools make it easy for you to cut through materials like sheet metal. If you need to get through metal fast, you’ll want an air cutting tool.
Impact Wrench and Ratchet
No matter your field, you’ve most likely come across stubborn nuts and bolts. With an impact wrench and ratchet, however, you can make easy work of loosening tough fasteners.
Air Dispensers
You could dispense grease manually. Still, why do it manually when you can use an air dispenser to distribute grease easily, cleanly, and simply? This air tool is ideal for shops that go through a large volume of grease every day.
Air Blasting
You’d use an air blasting tool to clean materials. You can also use it to remove surface paint, grime, and rust with ease.
Air Punch and Flange
With an air punch and flange, you can cut through and create holes in a variety of materials. Most often, shops use this air tool to work with metal.
Air Scarifier
An air scarifier enables you to remove surfaces from materials. You can also use an air scarifier to texture surfaces.
Air Stapler and Nailer
You won’t always find an air stapler or nailer in a garage. However, they’re among the most common and useful construction tools around.
Setting up a Pneumatic Tool System
Start with an air compressor to set up your pneumatic tool system. The air compressor compresses and stores air in its tank.
Air compressors come in many types, sizes, and capacities. Most importantly, you should consider the horsepower (HP) of an air compressor. The HP of an air compressor is the delivery rate measured in cubic feet per minute (CFM) or liters per minute.
You must also consider the tank air capacity in gallons or liters. Likewise, you should consider whether the air compressor gets powered by electricity or gas.
You must also consider the delivery rate of an air compressor. If you overlook this vital characteristic, you could end up with a compressor that can’t meet the flow rate demand for your shop. In other words, you’ll have to wait every so often for the tank to refill before you can use your air tools again.
Let’s go over some other things you should consider when setting up a pneumatic tool system.
Filter, Regulator, and Lubricator
The filter removes dust and water from the air. Dust can scour and damage to working parts of your air tools.
Eventually, dust can also cause your air tool system to clog. Over time, it will cause wear and poorly sealing surfaces, which will reduce the air pressure and, in turn, reduce power to the system.
The regulator serves as a faucet to control the pressure of air. It lets you adjust the power of your air tool up and down.
The lubricator makes a mist of small oil droplets in the airflow of your air tool system. The droplets lubricate the moving surfaces inside your tools.
Air Hose
You’ll also need an air hose to set up your pneumatic tool system. You’ll need one hose to connect the compressor to the filter/regulator/lubricator. You’ll need another hose to connect to your air tools.
When it comes to hoses, you have a couple of options. For example, you can purchase a coiled hose. A coiled hose curls up like the cord on a phone handset.
Alternatively, you can purchase a non-coiled hose. Manufacturers make these hoses using rubber or plastic.
Plastic is rigid, and it can crack over time. Rubber, however, is more flexible.
Air hoses also come in different internal diameters. If you’re using a tool that requires a large amount of air, it’s important to buy the right diameter air hose.
Regulating Air Pressure
Shops usually operate their air compressors at a set pressure. The pressure cut-out switch usually sets the pressure at around 8 to 10 bar.
You should always make sure your air compressor is working at its recommended setting.
In many cases, your air tool will have a lower max pressure compared to your air compressor. If you’re unsure, you can check the max pressure on the label of your tool.
You can also check the manual for your tool. With this information, you can set your air compressor regulator appropriately.
The Safety Relief Valve
The air compressor safety relief valve releases pressure when it becomes excessive. For example, you may have the pressure set too high. In these instances, the safety relief valve is your failsafe.
You should check your safety relief valve regularly. You must ensure that it’s operational and hasn’t seized up. Usually, you can identify the safety relief valve easily because it has a pull that looks like a key ring that allows you to release the pressure.
Know Your Fittings
Finally, remember to always check for BSP/NPT compatibility. Globally, most air equipment manufacturers use the BSP standard.
In the United States, however, most tools use the NPT standard. Both of these standards use inch measurements rather than metric ones.
However, NPT and BSP standards have different profiles. For example, they have different diameters for thread sizes and pitches. They’re incompatible for these reasons.
It’s possible that you could mate an NPT and BSP connection. However, the mating would result in a very poor seal. You would need an adapter to make the connection properly.
Also, you should consider sealing your fittings with Teflon tape, as you would with a plumbing fitting. To do so, you’d wind the tape clockwise, working from the entry point of the fitting. A few layers of Teflon tape will ensure a tight seal.
Level up With Pneumatic Tools Today
So, there you have it, a quick introduction to pneumatic tools and how they work. We’ve also given you a few tips on how to power your air tools and some of the benefits of using them.If you’re looking for precision control and safety combined with portability, Contractor Tool Supply has the perfect air tools for your operation. To see our entire lineup of professional-grade pneumatic tools, check out our inventory today.